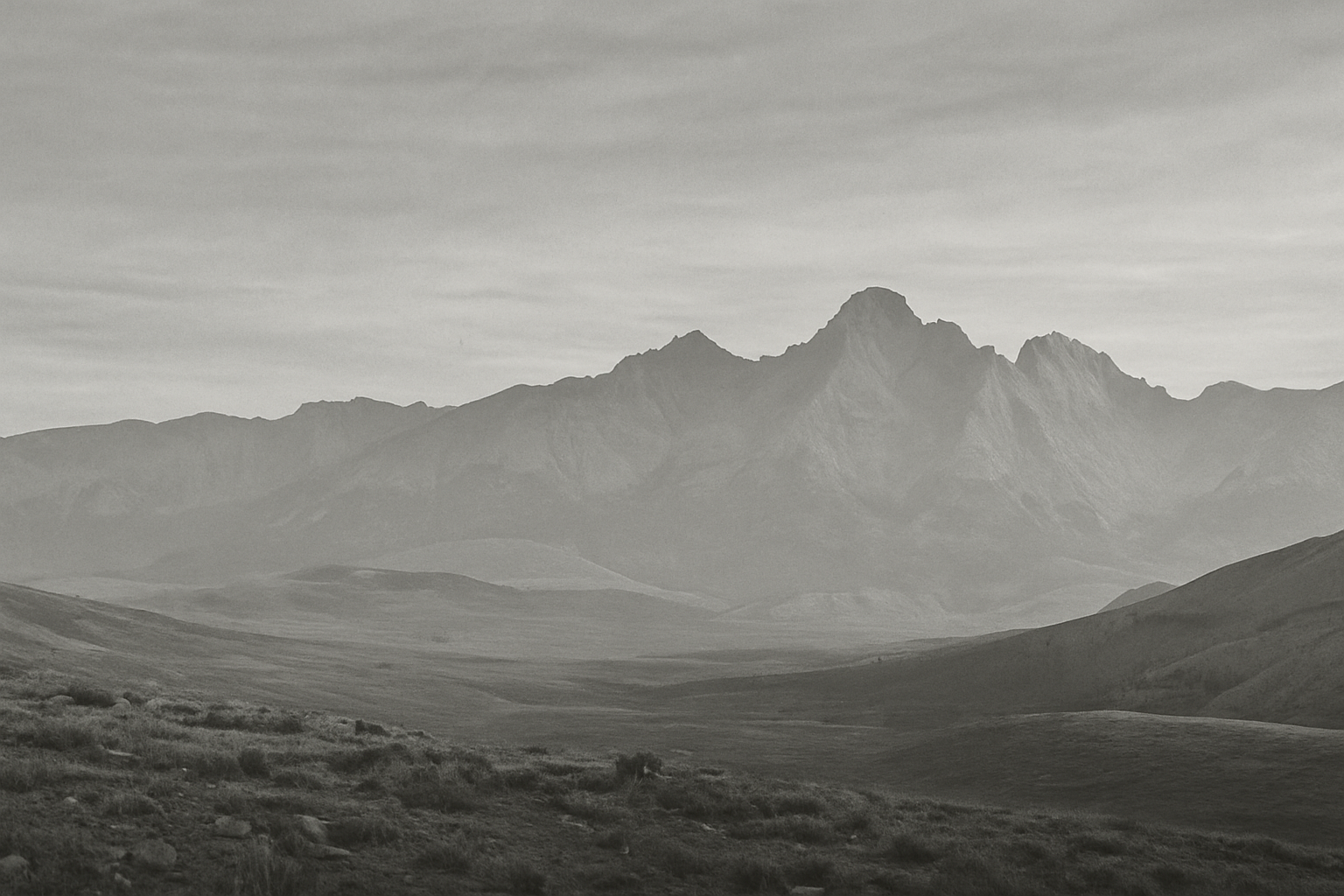
Industrial Parts & Rentals
Western Tough.
Precision-fit components and dispatch-ready equipment β fast quotes, same-day shipping, and no runaround.
Need a Fast Quote?
We'll get back to you within 1 hour β straight talk on parts & rentals.
Need a Fast Quote?
Parts or equipment rentalβwith a reply in under 1 hour.
Featured Products
Why Choose Us
Precision-Fit Parts
Built for uptime and fitment accuracy β no guesswork.
Same-Day Shipping
Fast fulfillment and delivery anywhere in the U.S.
Western Tough Support
We're technicians, not ticket bots. Real answers, fast.
Trusted Brands We Support
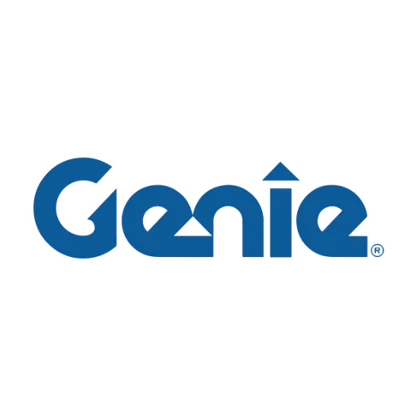
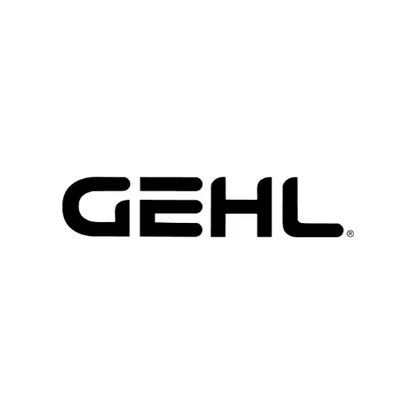
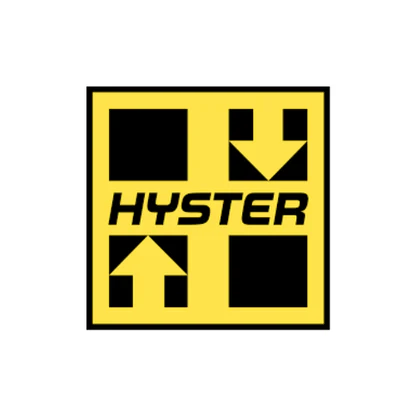
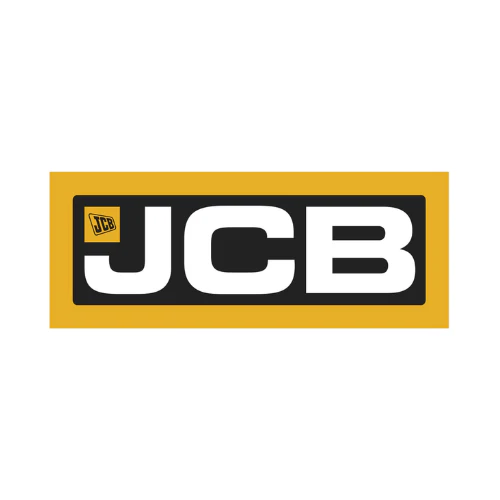
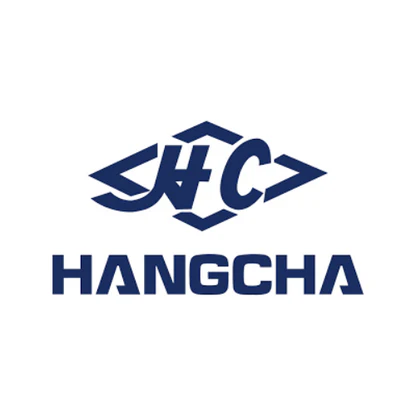
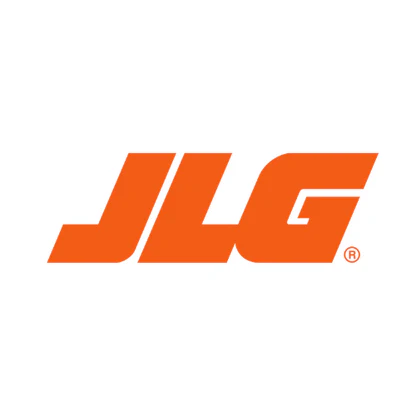
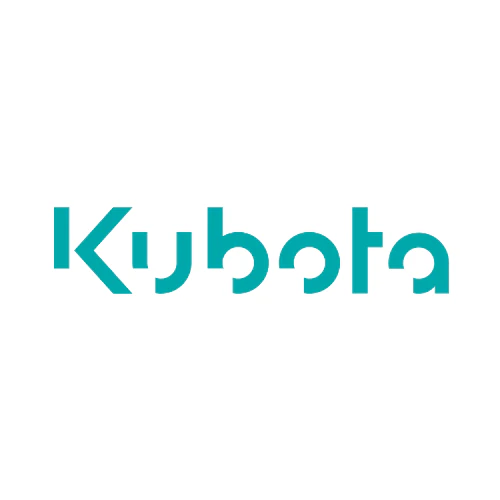
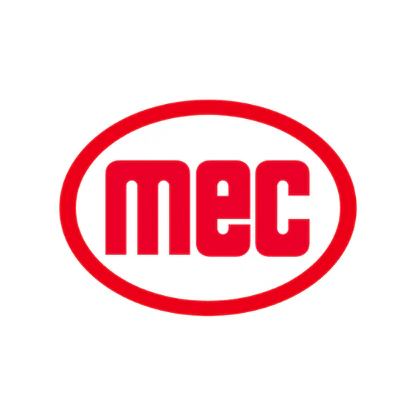
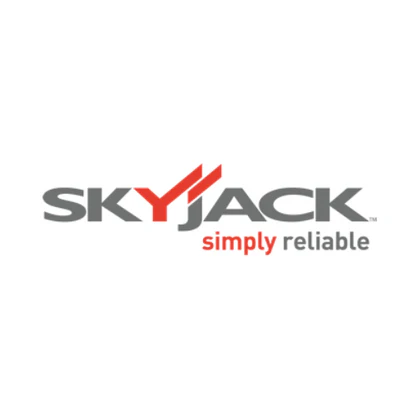
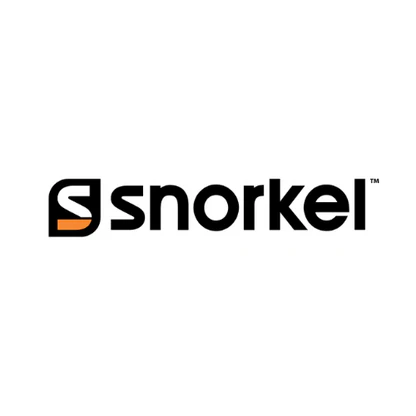
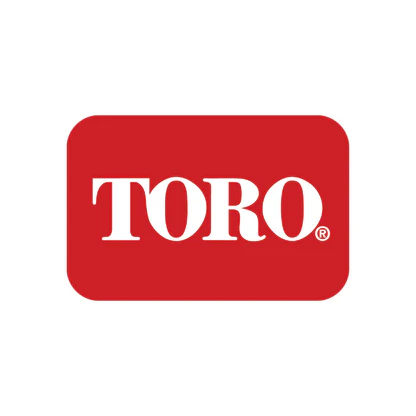
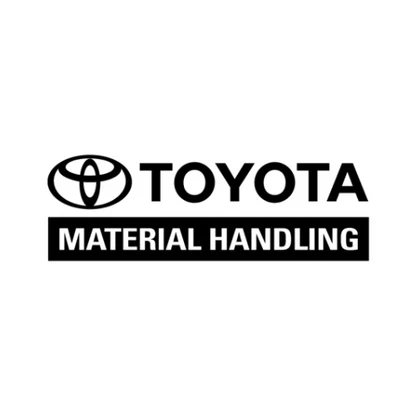
What Our Customers Say
"Flat Earth got us Genie parts overnight. No backorders, no nonsense."
β Fleet Manager, Montana
"Our warehouse lift was down. These guys had the joystick in stock and on a truck within hours."
β Maintenance Supervisor, Wyoming
"Parts arrived in 24 hours, fit perfectly, and cost less than OEM."
β Service Director, Colorado
Why Buyers Trust Flat Earth Equipment
Same-Day Shipping
Fast fulfillment and delivery anywhere in the U.S.
6-Month Warranty
Comprehensive coverage on all parts.
10,000+ SKUs In-Stock
Broad inventory across every major brand.
Regional Rental Partner Network
Local rental resources in WY, MT, NM & CO.
Prioritized U.S. Parts Vendors
Partnering with American suppliers for quality and speed.
Join the Flat Earth Fleet β Get Insider Access & Priority Service
Sign up to receive special access to bulk pricing, rental availability, and fleet-focused support from the Flat Earth Equipment crew.
Need Help Choosing the Right Part?
- β’ Not sure if a controller fits your Genie lift? We'll help you confirm compatibility.
- β’ Need fast forklift parts in Wyoming or Montana? We ship same-day from regional hubs.
- β’ Looking for a reliable scissor lift rental near you? Request a quote in 60 seconds.
Page last updated: May 2025